Halo beschermt F1-coureurs dankzij baanbrekende lastechniek
De halo is al weer een flink aantal jaren een essentieel onderdeel van het veiligheidspakket van de Formule 1. Deze cockpitbescherming is gemaakt van titanium en heeft zijn waarde al meerdere keren bewezen. Een baanbrekende lastechniek speelde een cruciale rol bij het sterk genoeg maken van de halo. Patrick Wouterse, oprichter en CEO van LKN WeldCompany in Amersfoort, vertelt erover in een interview dat onlangs is gepubliceerd op Motorsport.com.
Patrick Wouterse heeft met zijn bedrijf LKN WeldCompany een cruciale bijdrage geleverd aan het succes van de halo. Samen met zijn team heeft hij speciale laskamers gebouwd, zodat het lassen van titanium kan plaatsvinden in een atmosfeer van inert gas.
Het produceren van de halo vormde een grote technische uitdaging omdat deze moest voldoen aan de veiligheidsnormen van de internationale auto- en motorsportfederatie FIA. De halo moest het gewicht van een Londense dubbeldekkerbus kunnen dragen om Max Verstappen en zijn collega F1-coureurs de gewenste veiligheid te bieden. Hiervoor was niet alleen hoogwaardig titanium nodig, maar ook een foutloos, innovatief lasproces om de eigenschappen van het materiaal te behouden.
Het lassen van titanium
Eind 2017 hadden de bedrijven die deelnamen aan de aanbesteding van de FIA voor de productie van de halo – inclusief de partij die uiteindelijk het contract won – niet de technische capaciteiten in huis om de vijf titanium onderdelen van de halo te lassen met de hoogst mogelijke kwaliteit. Toen wendden ze zich tot LKN WeldTitan, de in titanium gespecialiseerde divisie van LKN WeldCompany. Na intensief onderzoek en ontwikkeling slaagden ze erin de onderdelen aan elkaar te lassen op een manier die de technische eigenschappen van het titanium volledig bewaarde, waardoor de halo voldeed aan de strenge FIA-normen.
“Titanium is een reactief metaal, wat betekent dat het reageert met elementen in de lucht – zelfs bij kamertemperatuur, in de zin dat oxidatie optreedt”, legt Patrick Wouterse uit in het gesprek met Motorsport.com. “Daarom is het zeer corrosiebestendig: zodra een dunne oxidelaag is gevormd, beschermt het het metaal tegen verdere oxidatie, een eigenschap die titanium ideaal maakt voor de chemische industrie.”
Verhouding sterkte-gewicht
Voor de halo was de belangrijkste eigenschap echter niet alleen corrosiebestendigheid, maar ook de sterkte-gewichtsverhouding. “Titanium, met name de grade 5-legering die voor de halo wordt gebruikt, is veel sterker dan staal en tegelijkertijd aanzienlijk lichter”, vervolgt Wouterse. “Waar je 15 mm roestvrij staal nodig hebt voor een bepaalde sterkte, heb je voor titanium misschien maar 5 mm nodig. Daarom wordt het veel gebruikt in de lucht- en ruimtevaart en is het gekozen voor de halo. Je wilt de sterkst mogelijke structuur zonder te veel gewicht aan de auto toe te voegen.”
Het lassen van titanium is echter een delicaat proces, omdat verhitting van het metaal ervoor zorgt dat het nog reactiever wordt, waardoor het elementen als zuurstof en waterstof opneemt als een spons in water. Zelfs de kleinste verontreiniging, zoals microscopisch kleine sporen van vuil of olie van een vingerafdruk, kan al rampzalige gevolgen hebben voor de sterkte van het titanium in het gebied waar de las zit. “Zodra titanium deze elementen absorbeert, verandert de samenstelling van het metaal en verzwakt het het drastisch, tot wel 75% in het aangetaste gebied”, zegt Wouterse. “Om dat te voorkomen, moet je een omgeving creëren waarin tijdens het lassen geen andere elementen het metaal kunnen bereiken.”
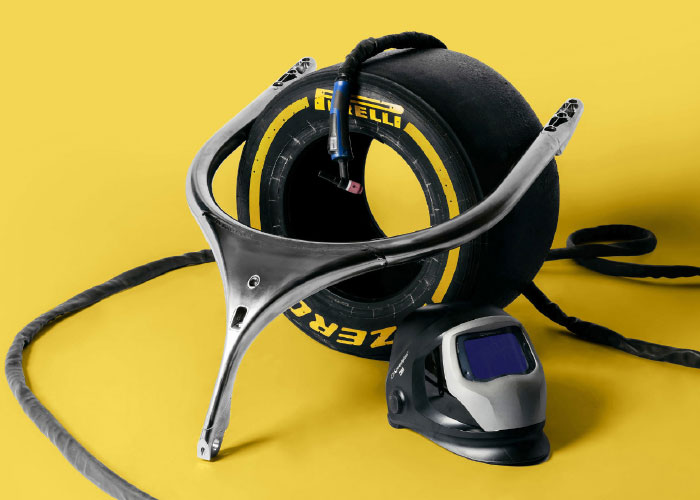
Voor de productie van de oersterke en tegelijk lichte halo was niet alleen hoogwaardig titanium nodig, maar ook een foutloos, innovatief lasproces om de eigenschappen van het materiaal te behouden.
Foutloos lasproces
Normaal gesproken beschermen lassers het gebied met een lokale stroom inert gas, zoals argon, om het gesmolten metaal af te schermen. Maar met titanium is dat niet genoeg. “De hitte straalt naar buiten — het omringende materiaal kan 1.000 graden Celsius bereiken. Maar bij slechts 150 graden begint titanium al zuurstof te absorberen”, verklaart Wouterse.
“Je kunt de schade echt zien — het titanium verandert van kleur. Zilver betekent dat de eigenschappen intact zijn, terwijl goud aangeeft dat er een zeer lichte maar acceptabele achteruitgang is geweest. Maar als het blauw, paars of groen wordt, is het materiaal in feite geruïneerd.”
Om dit probleem op te lossen, hebben Wouterse en zijn team jarenlang gewerkt aan het perfectioneren van een uniek lasproces. Ze hebben speciale laskamers gebouwd, zodat het lassen kan plaatsvinden in een atmosfeer van inert gas. “Het klinkt eenvoudig – doe de onderdelen in een doos en vul deze met argon – maar het is extreem complex”, zegt Wouterse. Het probleem is dat er altijd een kleine hoeveelheid zuurstof in de purgekamer achterblijft. “We vullen de kamer voornamelijk met argon, helium en neon. Maar argon is zwaar, zuurstof is licht en helium is nog lichter. Zelfs de geringste turbulentie van het bewegen van je handen in de handschoenen kan de gassen mengen en het zuurstofgehalte verhogen.”
“We moesten manieren vinden om de zuurstofconcentratie terug te brengen tot een paar delen per miljoen”, vervolgt Wouterse. “Alles, van de vorm van de kamer tot de afwerking van de wand, heeft invloed op het resultaat. Dat is dus allemaal heel ingewikkeld. En er zijn minstens vijftien andere variabelen die allemaal perfect moeten zijn om de juiste waarden te krijgen.”
Sterke reputatie
Wouterse heeft zich de afgelopen twee decennia gespecialiseerd in dit proces. Via LKN WeldCompany heeft hij een sterke reputatie opgebouwd, wat heeft geleid tot wereldwijde vraag naar de expertise van zijn bedrijf in gespecialiseerde lasprojecten in sectoren zoals lucht- en ruimtevaart, energie, chemie, kernenergie, farmacie en automotive. Daarnaast wordt Wouterse regelmatig ingehuurd door bedrijven voor procesontwikkeling en kwaliteitscontrole.
Nadat de halo-leverancier van de FIA via een wederzijdse connectie contact had opgenomen met LKN, ontwikkelde het bedrijf uit Amersfoort een op maat gemaakte laskamer die groot genoeg was om de hele halo-mal te huisvesten, rekening houdend met het complexe, asymmetrische holle ontwerp van de structuur. “Vervolgens hebben we het proces gekwalificeerd volgens EN ISO-normen, een prototype gelast en getest – het voldeed ruimschoots aan de normen van de FIA”, herinnert Wouterse zich. “Daarna zijn we snel overgegaan op productie. Uiteindelijk hebben we begin 2018 de eerste honderd halo’s voor de Formule 1 gelast.”