Het snelle graveerwerk, daar is Lion Laser echt goed in
Begonnen als aanbieder van lasergraveren en leverancier van Duitse en Chinese lasermachines is Lion Laser Systems in Breda in 15 jaar tijd uitgegroeid tot een volwassen producent van lasersystemen.
De zaken gaan goed. Het bedrijf groeit al jaren en dit jaar zit een omzetgroei van 50 procent er wel in. Dat is een fenomenaal percentage, maar toch houdt directeur/eigenaar Robert van Teeffelen deze ontwikkeling scherp in de gaten: “Want het moet hier wel leuk blijven voor iedereen. De mensen moeten mee kunnen groeien.” Ook voor zichzelf wil Van Teeffelen het leuk houden. Daarom is Karine Kanis onlangs gepromoveerd tot bedrijfsleider om de dagelijkse gang van zaken te regelen en aan te sturen. Zo kan hij zichzelf weer echt op de lasertechniek storten. “Ik blijf lasers fascinerend vinden. Het zijn magische gereedschappen. Ze werken helemaal contactloos. In één keer begint het te vonken en dan gebeurt er iets. Ik kan daar naar blijven kijken.”
Eigen machines bouwen
Naast de handel in lasermachines uit China – die Lion Lasers ombouwde tot machines die voldeden aan de CE-eisen en vervolgens leverde met service erbij – begon Van Teeffelen al snel met het ontwerpen van zijn eigen machines. Vrij vlot daarna maakte hij de keuze dat Lion Lasers uitsluitend nog leverancier zou zijn van volledig in Nederland gemaakte lasermachines. Daarom is ook de ondertitel Dutch Laser Machines aan de merknaam toegevoegd.
Snel graveren
Een specialisme van de Bredase machinebouwer is het snel graveren met galvo koppen. “En we zijn goed in maatwerk”, zegt Van Teeffelen. “Alles wat mensen met een laser willen, maken we voor hen op maat; met omkasting en indien gewenst automatisering.” Daarbij gaat het niet alleen om graveren. Lion Lasers heeft bijvoorbeeld ook machines voor het snijden van metaal gebouwd voor de TU Delft. En het bedrijf staat altijd open voor nieuwe toepassingen. “We krijgen wel een paar keer per maand vragen waarvan we zelf niet weten of het met lasers kan. Maar er kan veel. We graveren al tien jaar eieren. Appels en bananen kunnen we van codes voorzien. En zelfs het laseren van een bruine korst op brood is ons gelukt. Nikkelfolie ten behoeve van de vliegtuigbouw dat eerst werd geknipt met een handschaar wordt nu gesneden met een lasersysteem van ons. Momenteel onderzoeken we voor Tesla het reinigen van batterijen voordat ze worden gelast. Ook doen we onderzoek naar 3D graveren met UV-lasers. Dat ziet er veelbelovend uit maar het is een complexe materie om in de vingers te krijgen.”
Juiste techniek vinden
Binnen het bedrijf is alle kennis aanwezig om zulke vraagstukken op te pakken. “We kunnen zelf de software schrijven, de printplaten maken en de hardware ontwerpen.” De laserbronnen worden betrokken van producenten als IPG en Coherent. “Er zijn tal van lasertechnieken en het is best wel uitdagend de juiste techniek bij de juiste applicatie te vinden. Daarvoor heb je veel ervaringen nodig en je moet analytisch dingen kunnen onderzoeken. Het is geen makkelijk werk en zeker geen trucje dat je even kopieert. Maar met ons team van vijftien medewerkers kunnen we alles maken. Eerst weet je niet of iets kan, een paar maanden later heb je een machine waar een paar miljoen producten overheen gaan. Dat geeft echt een kick.”
Aluminium portemonnees
Van Teeffelen doelt daarmee specifiek op de samenwerking met Secrid, de producent van aluminium portemonnees. “Samen hebben we eerst een standaard lasersysteem van ons aangepast en geleverd, waarmee de eerste portemonnees zijn gegraveerd. Nu hebben ze vier volautomatische machines die op elke portemonnee een logo zetten en aan de binnenzijde een code als echtheidskenmerk. De eerste heeft al meer dan 3 miljoen portemonnees gegraveerd! Het snelle graveerwerk, daar zijn we echt goed in.”
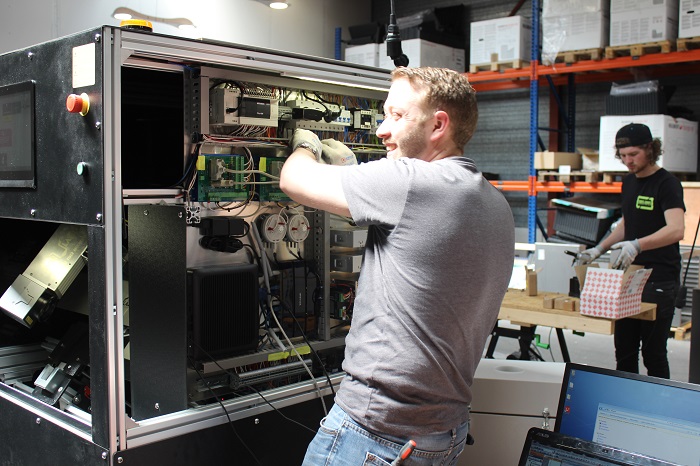
Montage, afstelling en keuring gebeurt altijd in eigen huis, want daarmee blijft de kwaliteit gewaarborgd.
Graveren is groeimarkt
Dat graveren is echt een groeimarkt. Ieder product moet tegenwoordig een identificatie hebben, track & trace is sterk in opkomst, logo’s en bijzondere kenmerken worden steeds vaker gevraagd. “Het verfraaien van producten door een bijzonder design of het aanbrengen van een fijne structuur is nu echt in opkomst. Het personaliseren van producten, zoals een naam op een pen, begint een steeds hogere vlucht te nemen. We ontwikkelen software om vanuit een webshop automatisch iets in een lasermachine in te stellen. Dan is het nog een product inleggen, de machine starten en produceren. Met automatisering erbij rolt alles achter elkaar uit de machine. We bouwen nu een systeem om het personaliseren van broodplanken terug te brengen van 15 naar 2 minuten per plank. Software is daarbij de key en wordt dus steeds belangrijker. We steken daar veel energie in. Dat moet ook wel: voor speciale toepassingen heb je ook speciale software nodig.”
Productie opvoeren
Lion Lasers voert een behoorlijk breed machineprogramma. “Onze machines zijn niet bijzonder groot, maar wat we maken is wel heel gespecialiseerd. De bronnen die we gebruiken hebben maximaal 1 à 1,5 kW vermogen, maar meestal veel minder. In de hogere vermogens voegen we niet veel toe aan de grote machinebouwers. Wij richten ons toch vooral op de speciale vragen.” Maar ook daarmee worden de machines toch steeds iets groter en ook complexer. Lion Lasers is onlangs begonnen met de bouw van een eerste nieuwe machine met een stalen frame van 200 kilo. “Voor onze werkplaats is dat een mega machine. Het eerste exemplaar bouwen we helemaal zelf op om te ontdekken wat we kunnen verbeteren. We lassen het frame zelf in elkaar en slijpen ook alles. Dat is een heel mooi proces.” De machine – met acht gestuurde assen die individueel kunnen worden geprogrammeerd in de software – is parametrisch ontworpen, zoals Lion Laser dat steeds meer doet. Zo kunnen eenvoudig de maten worden aangepast en kan er makkelijk en snel een special worden gebouwd, om het even met een kop voor snel graveren, een 3D kop of een kop om metaal te snijden. Zo wordt het makkelijker om de productie op te voeren. Van Teeffelen: “Dit jaar moet de groei komen uit meer standaard systemen. Onze capaciteit daarvoor is min of meer onbeperkt omdat we de productie van de onderdelen gemakkelijk kunnen uitbesteden. De montage, afstelling en keuring doen we altijd in eigen huis, want daarmee blijft de kwaliteit gewaarborgd. Daarnaast willen we hier in huis de kleine specials en een paar grote specials per jaar ontwikkelen en bouwen. Zo realiseren we onze groei en blijft het voor iedereen plezierig werken.”
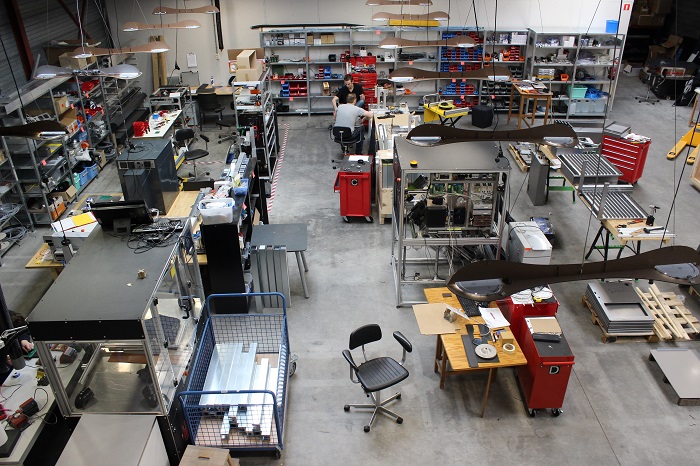
De werkplaats van Lion Laser.