Machinebouwers vullen digitalisering in met umati
Medio december organiseerde de Duitse branchevereniging voor werktuigmachinebouwers VDW een online beurs met diverse presentaties over umati – de universal machine technology interface. Onder andere Grob-Werke, Heller, Trumpf en United Grinding Group kwamen aan het woord om informatie te delen over het verbinden van verschillende machines en systemen met behulp van de standaard interface op basis van OPC UA.
De diversiteit aan machines en systemen in fabrieken is ontzettend groot. Het zijn niet alleen bewerkingsmachines, maar ook automatiseringsoplossingen, meetsystemen en -machines, systemen voor emulsiebeheer en gereedschapsbeheer et cetera. Al deze oplossingen hebben verschillende besturingen en interfaces, waardoor het duur en daardoor vaak onmogelijk is om ze allemaal met elkaar te laten communiceren in een overkoepelend IT-ecosysteem.
Dat terwijl de fabriek van de toekomst juist vraagt om een vergaande verbinding tussen alles machines en systemen om de voordelen van digitalisering optimaal te kunnen benutten.
Overkoepelend woordenboek
“Verschillende machines, besturingen en interfaces begrijpen elkaar niet. Met de open communicatiestandaard OPC UA wordt het al eenvoudiger om machines en systemen met elkaar te laten communiceren. Echter laat een open communicatiestandaard ruimte voor interpretatie. Ik vergelijk het altijd met een ingenieur die communiceert met bijvoorbeeld een advocaat. Beide spreken ze een taal zoals Engels, maar toch hebben ze een verschillende woordenschat. Helemaal als het op vakjargon aankomt. Daardoor is de communicatie tussen beide Engelssprekende partijen niet optimaal.
De moeizame communicatie tussen verschillende machines en systemen is met OPC UA niet anders. Met umati hebben we een oplossing ontwikkeld door als het ware een overkoepelend woordenboek samen te stellen, waardoor verschillende OPC UA communicatiesignalen worden omgezet in één standaard. Hierdoor wordt de uitwisseling van data tussen machines, componenten en installaties en hun integratie in IT-ecosystemen van klanten eenvoudig, naadloos en betrouwbaar”, vertelt Alexander Broos van VDW.
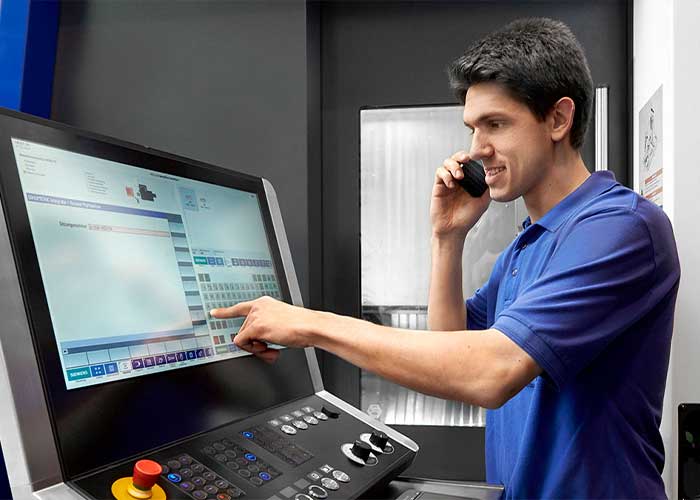
Dankzij de optimale integratie in netwerken kan Heller4Industry met behulp van umati de machineproductiviteit verhogen.
Plug & play
Umati is ontwikkeld door een grote groep machinebouwers met klanten die steeds vaker eisen dat machines eenvoudig en betrouwbaar in hun IT-ecosysteem kunnen worden geïntegreerd. Plug & Play is precies wat nodig is om de digitalisering vooruit te helpen. Om dit efficiënt te implementeren zijn open, onafhankelijke interfaces nodig. Tijdens het online event van VDW presenteerden diverse partners van de umati Core Group producten die gebruik maken van de functionaliteiten van de open interfaces van OPC UA en umati.
“Umati is een belangrijk puzzelstukje in onze strategie van digitalisatie. Wereldwijde standaards helpen niet alleen onze klanten, maar alle betrokken partners. Bovendien zijn ze een belangrijke basisvoorwaarde om de complexe uitdagingen van vandaag en morgen aan te kunnen”, zegt Philipp Liesenfeld van de United Grinding Group. Met acht verschillende machinemerken in het portfolio, weet deze producent als geen ander hoe belangrijk een gezamenlijke interface is. Daarom heeft het bedrijf een breed pakket aan ‘Digital Solutions’ ontwikkeld, zoals Remote Service, Service Monitor, Production Monitor en Customer Cockpit.
United Grinding heeft een eigen OPC UA server ontwikkeld voor alle merken binnen het platform. Deze server bestaat uit umati, een slijptechnologie dataset en klantspecifieke data. Binnen deze Digital Solutions speelt umati een grote rol om de inkomende data te standaardiseren. Liesenfeld: “Met umati kunnen we eindelijk transparantie in het proces verkrijgen en daardoor diensten met toegevoegde waarde, zoals voorspellend onderhoud, aanbieden. Hierdoor kunnen we de productiviteit bij onze klanten verhogen. Dankzij umati wordt het nu veel eenvoudiger om te starten met digitalisering. Waar een paar jaar geleden nog voornamelijk grote bedrijven investeerden in Industrie 4.0 oplossingen, zie je nu dat ook kleinere bedrijven de weg naar digitalisering weten te vinden.”
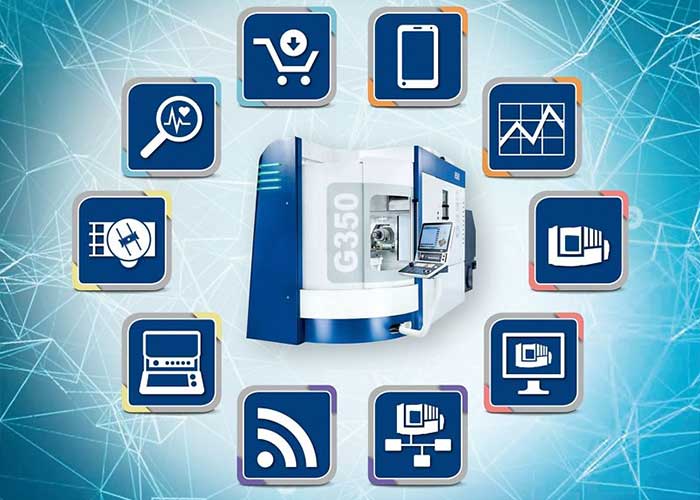
Diverse modules binnen Grob-NET4Industry stellen gebruikers in staat om directe en indirecte elementen rond het bewerkingsproces te beheren.
Synchroniseren in de cloud
Heller bidt met Heller4Industry een concept aan dat de productiviteit van bewerkingscentra verder verhoogt en zo een meerwaarde voor klanten genereert. “Dankzij de optimale integratie in netwerken kan Heller4Industry met behulp van umati de machineproductiviteit verhogen en uitgebreide functionaliteiten, servicepakketten, complementaire machinefuncties en ‘on-demand’-diensten aanbieden”, vertelt Stefan Geiger. Het Heller4Industry-concept, dat uit drie modules bestaat, illustreert het belang van eenvoudige bediening, individuele werkstukproductie en uitgebreide data-analyse.
Afhankelijk van de wensen en netwerkmogelijkheden bij de klant, kan Heller drie mogelijkheden aanbieden. De meest eenvoudige oplossing is Heller4Operation. Dit is een gebruiksvriendelijke interface voor Heller-bewerkingsmachines die de data bij de machine sorteert en inzichtelijk maakt in een browser. De tweede module is al een stuk uitgebreider omdat deze data verzamelt van meerdere machines in een bedrijf. Heller4Services werkt met een dataserver bij de klant die alle data synchroniseert en alle machines overzichtelijk weergeeft. De Services-interface concentreert zich op transparantie in productie-, onderhouds- en serviceprocessen gedurende de gehele levenscyclus van de machine.
Deze module vormt de basis van evaluaties en statistieken en helpt zo de stilstand van machines te verminderen. Ook maakt het visualiseren van specifieke machinestatusinformatie, zoals statusweergaven van assen, spillen of andere samenstellingen, het mogelijk om de slijtagetoestand te bepalen. De derde module, Heller4Performance, geeft de mogelijkheid om data van alle machines in verschillende fabrieken te synchroniseren in een cloudomgeving.
Met deze oplossing is het mogelijk om overal real-time inzicht te krijgen in alle belangrijke procesdata. Deze data kan vervolgens gebruikt worden voor machine-analyses voor proces- en prestatieoptimalisatie.
Open cloudplatform
Grob gebruikt umati om een optimale verbinding te maken tussen verschillende systemen en het cloud4machine cloudplatform. Hierin komen een tiental digitaliseringsmodules van Grob samen. Deze NET4Industry modules zijn ontwikkeld om te voldoen aan de behoeften van Industrie 4.0 op een manier die flexibel en productief is. De modules stellen gebruikers in staat om directe en indirecte elementen rond het bewerkingsproces te beheren om zo bewerkingsmachines productiever te maken.
Van productieplanning, bewaking en analyse tot aan de visualisatie van bewerkingsprocessen en proactief onderhoud, alle productiefacetten zijn geïntegreerd. Bovendien zijn Grob-NET4Industry-modules uitgerust met umati, met als doel fabrikantonafhankelijke digitaliseringsconcepten te implementeren en projectondersteuning te bieden aan alle klanten.
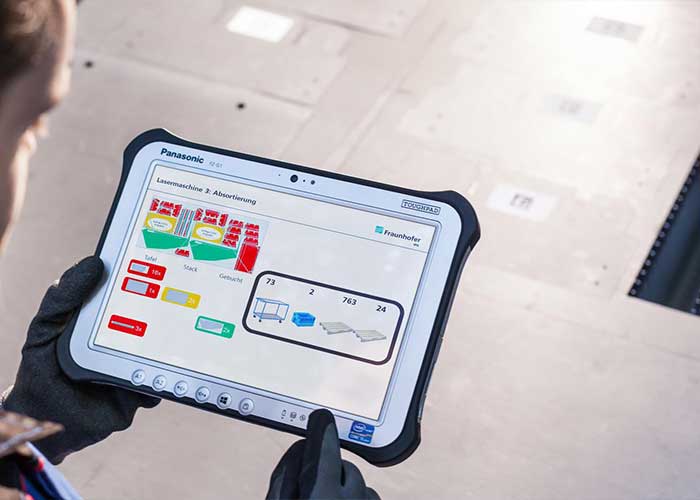
Met TruTops Monitor van Trumpf kunnen gebruikers meer transparantie verkrijgen in het productieproces.
Transparantie in productieproces
Een bedrijf dat al ver voor umati de weg naar digitalisering is ingeslagen is Trumpf. “We zijn ons al lang bewust dat met digitalisering meer transparantie in het productieproces kan worden gebracht. Hierdoor wordt het eenvoudiger om gericht te optimaliseren. We gebruiken bijvoorbeeld al 5 jaar OPC UA. Voor de evolutie van Industrie 4.0 moet er een standaard zijn om machines op dezelfde manier te verbinden, onafhankelijk van de fabrikant. En dat is Umati.
Omdat onze klanten niet alleen machines en systemen van Trumpf in bedrijf hebben staan, was het voor ons een logische stap om nauw betrokken te zijn bij de ontwikkeling van umati”, vertelt Tobias Grass van Trumpf. Volgens Trumpf kan transparantie in het proces zorgen voor meer winst door kosten te verlagen of de output te verhogen. Door gebruik te maken van alle data uit het productieproces kunnen machinestoringen en schrootproductie worden voorkomen, doorlooptijden en zoektijden worden verkort en productiekosten worden verlaagd.
Volgens Grass weten veel producenten niet hoeveel tijd hun machines daadwerkelijk produceren. “De verwachting is vaak heel anders dan de realiteit. Zo hadden we een klant die dacht dat zijn machinepark 75% van de tijd produceerde. In de werkelijkheid was dit slechts 46%. Door chaos in de productie, maar ook door te programmeren aan de machine, was de output vele malen lager dan verwacht. Met digitalisering krijg je meer inzicht in het proces en kun je problemen eenvoudig identificeren en die snel oplossen.”