Next level machinetransport
‘We hebben een grote jongen verkocht’. Dat waren de woorden van Ron Kentrop van Okuma Benelux, toen hij Dennis Oorschot van Jan van Dam Transport belde voor een nieuw project. Met dat telefoontje werd een traject in gang gezet dat resulteerde in de vlekkeloze plaatsing van een grote 5-assige freesmachine met een totaal gewicht van maar liefst 75 ton bij Witec in Stadskanaal. Ook hier bleek maar weer eens: een goede voorbereiding is het halve werk.
De medewerkers van Jan van Dam plaatsen de machine zodanig, dat de monteurs van Okuma er meteen mee aan de slag kunnen.
Jan van Dam vervoert al een aantal jaren alle machines die Okuma Benelux bij klanten in ons land, België en Luxemburg installeert. De reden hiervoor is simpel: vertrouwen. “Ik hoef niet meer na te denken over het transport van een machine, omdat ik weet dat het wel goed zit”, zegt Stephan Slingerland van Okuma Benelux.
Grootste 5-asser van Okuma
Hij heeft namens Okuma de machine bij Witec verkocht. Het is een MU-10000H, de grootste 5-assige freesmachine van de Japanse machinefabrikant. Een heel bijzondere machine omdat hij ondanks de afmetingen en het gewicht werkstukken tot maar liefst 2500 kilo even dynamisch en nauwkeurig kan bewerken als de machines met wat meer gangbare formaten van Okuma. Er staan vier van deze machines in Europa, waarvan nu twee in Nederland.
Het transporteren van zo’n machine naar de klant is dus ook heel bijzonder. Stephan: “Dat merkte ik al aan de chauffeurs van Jan van Dam die ik in het veld regelmatig tegenkom. Het leefde echt bij hen en ze keken ernaar uit om deze klus te doen.”
Stap voor stap afpellen
Het grote vertrouwen in de capaciteiten van Jan van Dam betekent niet dat Okuma het project helemaal uit handen geeft en er niet meer naar omkijkt totdat de machine op zijn plek staat. Integendeel, het hele transport is een nauwe samenwerking tussen leverancier, transporteur en eindgebruiker, in dit geval Witec. Samen hebben ze van tevoren een strak plan gemaakt. “We pellen zo’n project helemaal af; stap voor stap”, zeggen Jan van Dam en Dennis Oorschot. “Daarbij luisteren we mega-goed naar de klant. Als je zijn wensen kent, kun je hem goed adviseren.”
Grote operatie voor Witec
In dit geval begon het project met een bezoek van Jan van Dam samen met Ron Kentrop en Tom Strijbos van Okuma aan Witec om de situatie ter plaatse op te nemen en een eerste vergadering te beleggen. De komst van deze kolossale machine betekende ook een grote operatie voor Witec, dat hiervoor een team van zes mensen had geformeerd. Om ruimte te maken voor de 5-asser is het bedrijfspand verbouwd en een magazijn verhuisd. Er is een nieuwe ingang gebouwd waardoor de verschillende machinedelen naar binnen konden en de vloer van de route waarlangs deze onderdelen naar hun plek zijn gebracht, is verstevigd. Ook zijn de stroomvoorziening en de fundering aangepast.
Uitpakken machinedelen
Jan van Dam heeft een plan gemaakt om de zware machinedelen probleemloos door de fabriek te vervoeren en op hun plek te zetten. Speciale aandacht was er hierbij voor het uitpakken. De in Japan geproduceerde 5-asser stond al in tien stalen kisten in het havengebied van Antwerpen in opslag. Een voor de hand liggende optie was om deze kisten rechtstreeks naar Stadskanaal te brengen en ze daar uit te pakken. Maar bij Witec was daarvoor niet veel ruimte. Het zou buiten moeten gebeuren en veel tijd kosten, met alle risico’s van regen en wind.
Het team van Jan van Dam stelde daarom voor de kisten met de machinedelen eerst naar het warehouse van zusterbedrijf Jan van Dam Global Machine Logistics in Rotterdam te brengen en ze daar uit te pakken. Dat bood verschillende voordelen: de kisten konden binnen worden uitgepakt onder ideale omstandigheden. De tijdwinst bij Witec zou groot zijn. “Bovendien heb je daar helemaal geen afval. Dat komt veel professioneler over”, aldus Jan van Dam.
Geavanceerd materiaal en deskundigheid
Maar de kostbare machinedelen zitten natuurlijk niet voor niks in stevige stalen kisten. Die dienen ter bescherming tijdens het transport. Als je ze uitpakt en dan gaat vervoeren, moet dat wel op een veilige manier kunnen. Daar heeft Jan van Dam geavanceerd materiaal voor. Speciale, verbreedbare trailers, waarin machines zonder risico kunnen worden vervoerd. “Deze trailers zijn zo goed, dat het steeds gemakkelijker wordt om het op deze manier te doen”, zegt Dennis Oorschot. “Minstens zo belangrijk daarbij is de ervaring en de deskundigheid van onze medewerkers. Ze weten voor wat voor apparatuur ze verantwoordelijk zijn en hoe ze daar mee om moeten gaan. Dat geldt voor de mensen die de machines in het warehouse uitpakken, de chauffeurs en de medewerkers die hem bij de klant neerzetten.”
“Met de capaciteit van onze medewerkers en ons materiaal zorgen wij voor next level machinetransport”, vult Jan van Dam aan.
Op stelvoeten gezet
Dankzij alle voorbereidingen konden het transport en de plaatsing in drie dagen worden uitgevoerd. Hierbij zijn drie diepladers en twee trailers ingezet, die allemaal na elkaar, exact op tijd, bij Witec arriveerden. Stephan Slingerland was er bij toen de eerste vrachtwagen aankwam. “Het onderdeel werd er met de kraan af gehaald en naar binnen gebracht. Dat was in een mum van tijd gebeurd.” Daarna kwamen de vrachtwagens met de overige delen. Die werden precies in de goede volgorde naar binnen gebracht, zodat ze direct op goede plek konden worden gezet. Dat gebeurde met robotmovers, die machines tot op de millimeter nauwkeurig kunnen neerzetten.
In de productieruimte van Witec is eerst het zwaarste machinedeel van 30 ton op z’n plek gezet en verankerd. Daarna volgden de overige delen. Ze zijn door de medewerkers van Jan van Dam op stelvoeten gezet en al grof geleveld, zodat de monteurs van Okuma er meteen mee aan de slag konden. In een kleine vijf weken hebben ze de machine vervolgens helemaal opgebouwd.
Durf partners te zijn
Alle betrokkenen kijken terug op een zeer geslaagd project, waarbij ze het belang van samenwerking en een goede voorbereiding onderstrepen. “Durf partners van elkaar te zijn”, zeggen Jan van Dam en Dennis Oorschot. “Schakel allemaal lekker op tijd. Dan zit er geen stress op en loopt zo’n project gesmeerd. Daar wordt iedereen enthousiast van.”
Ook Stephan Slingerland van Okuma benadrukt het belang van goed voorwerk. “Dan gaat zo’n machine fluitend naar binnen.”
Het team van Witec kijkt eveneens heel tevreden terug op de machineplaatsing. “We wisten dat we een bijzondere machine kregen, die een heel andere benadering vroeg dan de installatie van andere machines”, zegt Raimon Warta, CTO van Witec. “We zijn zeer tevreden over Jan van Dam en Okuma. Alles is ontzettend goed voorbereid en hun medewerkers vormden echt een ingespeeld team. Het zijn professionals en die heb je nodig om zo’n enorm project voor elkaar te krijgen. Het liep allemaal van een leien dakje.”
‘The beast’ produceert extreem rein en nauwkeurig
De grote 5-assige freesmachine van Okuma is inmiddels operationeel bij Witec. Of, zoals CTO Raimon Warta eind juli aan zijn volgers op LinkedIn meldde: “The Beast is in production.” De machine is volgens hem en zijn collega Jaap Siems, technisch commercieel adviseur, uniek gezien de grootte en de nauwkeurigheid. “Machines van dit formaat zijn vaak gebouwd volgens het gantry-principe. Daarmee verlies je nauwkeurigheid. Maar deze machine heeft een tuimel-kanteltafel. Hierdoor kunnen we binnen het µm-bereik bewerken.”
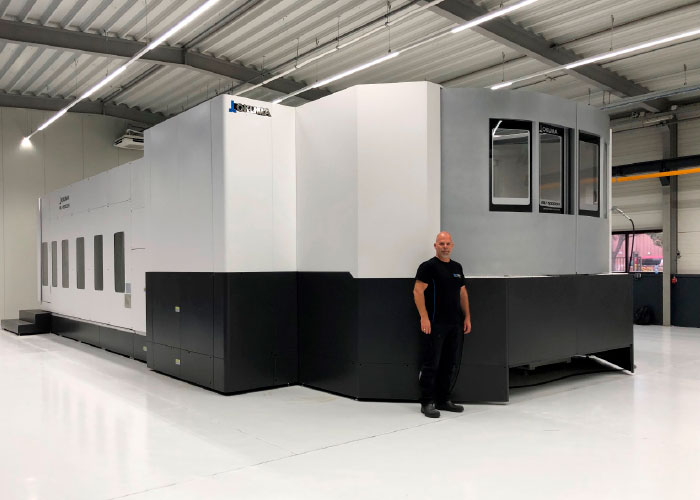
Aan de Witec-medewerker voor de machine is goed te zien hoe groot de Okuma MU-10000H is.
De Okuma MU-10000H is veel meer dan een 5-assig horizontaal high-speed bewerkingscentrum. Het is een complete temperatuurbeheerste cel, die geschikt is voor onbemande productie. De bewerkte onderdelen worden direct gemeten (black light inspectie en UV-inspectie) en gecleand. Hierdoor hebben de onderdelen die van de machine afkomen naast een extreme nauwkeurigheid ook een extreme reinheid. Witec heeft dat nodig voor de productie van vacuümdelen voor onder meer systemsuppliers, de semicon, de food en defensie.
Bijzonder hierbij is dat de machine veel verschillende delen door elkaar heen kan produceren. Daarom is de 5-asser uitgerust met een groot gereedschappenmagazijn met 176 posities. De werkruimte van de machine (X-as = 1550 mm, Y = 1600 mm, Z = 1650 mm) kan worden benut voor het bewerken van één groot onderdeel, maar meervoudig opspannen is eveneens mogelijk.