Persdelen voor kleine series duur? Proven Concepts bewijst het tegendeel
Proven Concepts heeft haar sporen ruimschoots verdiend met het 3D vormen van onderdelen voor de automotive industrie. Maar de ontwikkelaars in Valkenswaard, die ideeën zichtbaar maken, kunnen ook veel betekenen in andere industrieën. Zoals de medische en agrarische sector en de consumentenartikelen. Ze willen het persen meer onder de aandacht brengen, omdat uit één plaatdeel vaak hele mooie en functionele vormen kunnen worden gemaakt; zonder het traditionele kanten en lassen.
Proven Concepts beschikt over twee persen: een 400 ton hydraulische dieptrekpers met een bed afmeting van 2100 x 1300mm en een 100 ton pers voor klein dieptrekwerk.
Dat geldt ook voor prototypes, enkelstuks en kleine series, maar veel mensen in de industrie zijn zich daar niet van bewust. Want de overheersende gedachte is nog altijd dat er voor persen speciale gereedschappen moeten worden gemaakt, hetgeen tijdrovend en duur is.
Hierdoor zou persen alleen een interessante techniek zijn voor de productie van grote series. “Wij merken bovendien dat de huidige generatie constructeurs minder kennis heeft van het 3D vervormen van plaatmateriaal. Dus kijken ze bij het ontwerpen van hun producten al gauw naar het kanten en samenstellen van verschillende delen”, zeggen directeur Gerard Maessen en operationeel directeur Ron Cornelissen van Proven Concepts.
Esthetisch mooiere vormen
Zij betreuren dat. De twee zijn echte techneuten; oude rotten in het vak met een open blik voor de ongekende mogelijkheden van moderne technieken en intelligente software, maar tegelijk ook gezegend met een scherp oog voor wat de beste en meest logische productietechniek is. Met hun bedrijf zijn ze door jarenlange ervaring en bewezen concepten uitgegroeid tot een toonaangevende speler in productontwikkeling, model- en protobouw. In de veeleisende automotive sector bewijst Proven Concepts al 20 jaar dat 3D geperste vormen vaak een uitstekende oplossing zijn.
En Maessen en Cornelissen zijn ervan overtuigd dat dit ook geldt voor andere industrieën. “Heel veel behuizingen bijvoorbeeld zijn kantdelen die worden gelast of gelijmd. Door 3D vormen kun je een product een esthetisch mooiere vorm geven. Door het vervormen van plaatwerk en het aanbrengen van verstevigingrillen kun je dunnere materialen inzetten en zodoende gewicht reduceren. Het levert ook een voordeel op voor de food- en medische industrie.
Deze producten kunnen makkelijker worden schoongemaakt doordat ze voorzien zijn van afgeronde hoeken zonder lasnaden. Ook kun je met persen kosten besparen. Ja, het klopt dat je daar gereedschap voor nodig hebt. Maar door snel te kunnen ontwikkelen en een gereedschap te kunnen maken, zonder alle extra’s die er nodig zijn voor een seriegereedschap, en eventueel met een klein hulpgereedschap, kunnen we deze kosten zeer laag houden te opzichte van een serieproces. Bovendien verdien je de gereedschapskosten terug in andere fases van het totale proces.”
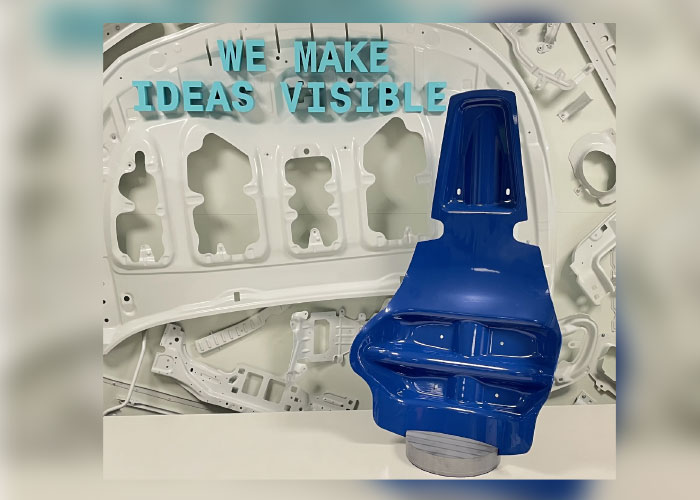
Dit aluminium schaaldeel vormt de basis voor de zitplaatsen in de rollercoasters van Vekoma. Hiermee is een lasconstructie vereenvoudigd naar één product, dat stabiel en veilig is
Alles in eigen huis
Een rondgang door het bedrijfsgebouw in Valkenswaard onderstreept de woorden van Maessen en Cornelissen. Die voert niet alleen langs de werkplekken van de engineers, de persen, de verspanende afdeling met allemaal 5-assige bewerkingscentra en hoogwaardige meet- en analysefaciliteiten, maar ook langs stellingen met tal van voorbeelden die in de afgelopen jaren zijn ontwikkeld en geproduceerd: heel veel body-, interieur- en exterieurdelen voor de automobielsector.
Want dat is kerncompetentie van Proven Concepts. Het bedrijf heeft alle faciliteiten in eigen huis om klanten bij het maken van deze producten van a tot z te begeleiden. Het team kan een compleet ontwikkelingspakket aanbieden om de ideeën van klanten te transformeren in zichtbare oplossingen; vanaf het allereerste conceptidee tot en met het maken en leveren van het product, inclusief meetrapport.
Proven Concepts doet zowel de engineering van het product en het gereedschap, als ook het maken van het gereedschap en het product. Het bedrijf beschikt hiervoor over twee persen, een 400 ton hydraulische dieptrekpers met een bed afmeting van 2100 x 1300mm en een 100 ton pers voor klein dieptrekwerk. Daarbij is er een nauwe samenwerking met een aantal vaste partners voor processen als 3D laserlassen, coaten en het nabehandelen van producten. Zo worden de doorlooptijden heel kort gehouden. “Kosten en korte doorlooptijden zijn onze belangrijkste doelen in de prototype fase”, zegt Ron Cornelissen.
Aluminium schaaldeel
Proven Concepts heeft ook al diverse projecten buiten de automotive sector op haar naam staan. Een mooi voorbeeld zijn de aluminium schaaldelen die de basis vormen voor de zitplaatsen in de rollercoasters van attractiebouwer Vekoma. “Deze worden gemaakt uit 3 mm dik plaatmateriaal dat we vervormen en nadien met zacht materiaal omgieten. Zo hebben we een lasconstructie kunnen vereenvoudigen naar één product, dat stabiel en veilig is.”
Complexe vraagstukken
De technische vraagstukken waarvoor Proven Concepts wordt ingeschakeld mogen best complex zijn. Graag zelfs. “We willen graag in de conceptfase van producten meedenken. Onze sterkte is dat we van meerdere technieken kennis en kunde hebben. Zo kunnen we bijvoorbeeld meedenken of delen kunnen worden samengevoegd waardoor minder materiaal wordt gebruikt en minder producten geproduceerd hoeven te worden. Of wat er in staal en wat er misschien in kunststof moet. Ook met hybride delen, bijvoorbeeld stalen delen die met een thermoplast worden omspoten hebben we ervaring. Evenals met vezelversterkte materialen, die in matrijzen 3D kunnen worden vervormd. Ook dat is heel interessant met het oog op de tendens naar lichtgewicht delen.”
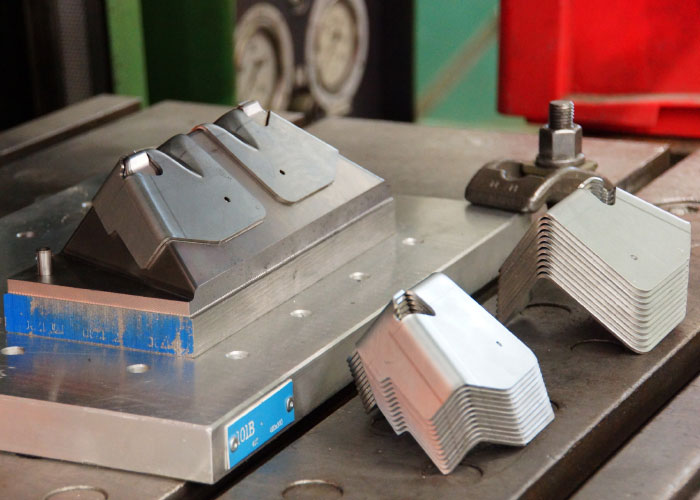
Indien nodig, worden er verstevigingen aangebracht op een product.
Meer bekendheid voor persen
Centraal staat voor Maessen en Cornelissen dat de bekendheid van het persen omhoog moet. “Proven Concepts verlaagt drempel naar persdelen voor kleine series”, zeggen ze. “Mensen in de industrie moeten weten dat we met persen heel veel kunnen bereiken wat niet kan met kanten en samenstellen.”