Recycling gegalvaniseerde onderdelen met schokgolven
Het recyclen van gegalvaniseerde onderdelen is een uitdaging. Omdat het terugwinnen van de materialen die ze bevatten technisch complex is, concentreren recyclingprocessen zich over het algemeen slechts op één van de materiaalfracties – meestal de metalen. De resultaten van deze processen bereikten een lage materiaalzuiverheid, wat betekende dat alleen downcycling van componenten mogelijk was. Deze twee factoren maakten het kostbare en omslachtige recyclingproces economisch nauwelijks rendabel in verhouding tot de waarde van het teruggewonnen materiaal.
Bij sanitairfabrikant Hansgrohe is een eigen ontworpen installatie in gebruik genomen voor het strippen van verchroomde kunststof onderdelen door middel van shockwave-behandeling, in combinatie met voorversnipperen en magnetische scheiding.
ImpulsTec heeft echter de schokgolf- of elektrohydraulische fragmentatietechnologie geïmplementeerd voor het scheiden van complexe materiaalverbindingen in industriële processen. Bij sanitairfabrikant Hansgrohe is een op maat gemaakte installatie in gebruik genomen voor het strippen van verchroomde kunststof onderdelen door middel van schokgolfbehandeling, in combinatie met voorversnipperen en magnetische scheiding. Deze installatie kan het productieafval in bad- en keukenkranen scheiden met een resulterende materiaalzuiverheid van > 99,8 m%. Dat maakt het mogelijk om beide materiaalfracties te hergebruiken in hoogwaardige componenten.
Doorn in het oog
Omdat de Hansgrohe Groep hoge kwaliteitseisen stelt aan douche-, bad- en keukeninrichtingen, is een zekere mate van productieverspilling onvermijdelijk. “Vroeger waren de verchroomde ABS-kunststof onderdelen een doorn in het oog”, zegt David Zapf, specialist voor oppervlaktetechniek bij Hansgrohe, over de behuizingen voor bijvoorbeeld handdouches. Om zijn producten de nodige robuustheid en duurzaamheid in gebruik te geven, creëert de fabrikant een stabiele verbinding tussen kunststof en metaal.
Enerzijds is dit een indicator van kwaliteit, maar anderzijds brengt het grote uitdagingen met zich mee voor de opwerking, zoals Zapf meldt. “Omdat het voor ons tot nu toe niet mogelijk was om de dunne galvanische laag intern van het ABS te scheiden met behoud van beide materiaalfracties, hebben we vóór dit project verchroomde onderdelen overgedragen aan externe recyclingpartners.”
Zapf kwam in contact met de shockwave-technologie van ImpulsTec, die herstel van beide materiaalfracties met een hoge zuiverheidsgraad beloofde. De twee bedrijven werkten samen aan een procedure voor het strippen van de gegalvaniseerde kunststof onderdelen. Om dit te doen, combineerden ze de schokgolfbehandeling met pre-shredding en daaropvolgende magnetische scheiding. Sinds begin 2024 is de installatie bij Hansgrohe in bedrijf.
Proefinstallatie
“Vanwege de omstandigheden ter plaatse moest de nieuwe installatie geschikt zijn voor plaatsing buiten en niet langer zijn dan 22 m en niet breder zijn dan 10 m”, legt ImpulsTec-directeur Stefan Eisert uit. “Daarom hebben we de pilotfaciliteit zo ontworpen dat deze werkt in drie weerbestendige containerunits.” Omdat de te recyclen gegalvaniseerde onderdelen van verschillende afmetingen en complexiteitsniveaus zijn, is de eerste container geschikt voor het voorversnipperen en bevat deze een zeefkolom. Het homogene granulaat dat in dit proces wordt verkregen, wordt in de tweede fase onderworpen aan een gepatenteerde schokgolfbehandeling.
Hierbij wordt de voorbehandelde grondstof in een waterbad gedaan; Een korte ontsteking van een elektrische boog tussen twee elektroden in het medium veroorzaakt mechanische schokgolven die de afzonderlijke materiaalfracties geleidelijk van elkaar scheiden.
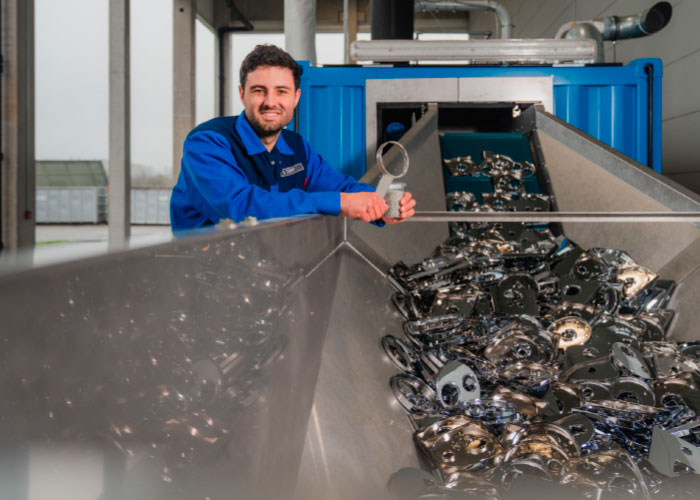
“Dankzij elektrohydraulische fragmentatie kunnen we nu 98% van de grondstoffen uit ons productieafval in dit gebied hergebruiken ”, zegt David Zapf, procesingenieur voor kunststoftechniek en oppervlaktetechniek bij de Hansgrohe Groep.
Het gebruikte water wordt gefilterd en vervolgens in een gesloten kringloop teruggevoerd naar het schokgolfproces. Het nabewerkingsmateriaal wordt naar de derde container getransporteerd en daar gedroogd. De afzonderlijke materiaalfracties worden vervolgens gescheiden door middel van magnetische scheiding. Het grootste deel hiervan – 70 tot 80 procent – is plastic. Om bruikbaar te zijn voor premium nieuwe producten, moet het een stabiele zuiverheid hebben van > 99,8 m%. De resterende materiaalfractie bestaat uit koper, nikkel en chroom uit de galvanische coating, die wordt geleverd aan metaalverwerkende bedrijven. “Omdat deze faciliteit een nieuw concept is, moesten we in de loop van de ontwikkeling alle processtappen en hun onderlinge koppeling en interactie grondig uitproberen en optimaliseren. Daarmee kunnen we nu voldoen aan de hoge eisen van Hansgrohe op het gebied van materiaalzuiverheid”, verklaart Eisert.
Nieuwe mogelijkheden
Hansgrohe onderzoekt nu al in hoeverre de shockwave-technologie in de toekomst ook kan worden gebruikt voor de recycling van complete producten, d.w.z. kranen die al door klanten zijn gebruikt. “De toepassing van ons nieuw ontwikkelde stripproces voor sanitaire producten was slechts de eerste stap”, concludeert Eisert. “Zowel in de auto-industrie als in de elektronicasector opent onze technologie ook nieuwe mogelijkheden. Zeker voor het hergebruik van productieafval en productcomponenten aan het einde van hun levenscyclus.”